Company Overview
Revex Group is a new-age chemical company with a strong presence of over four-decade across India. The company started in 1981 has now become one of the leading manufacturers in India having manufacturing units in Bhiwadi and Chopanki (Rajasthan). Revex Group has diversified its roots into FRP Pigments, Glass Fibre, Rotogravure Inks, Heat Seal Adhesives, Mould Release Agents, Accelerators and Catalysts.
SAP Business One implemented by Uneecops, works very well for us! We have been assisted by their team whenever needed.
Rohit Santoshi,
SAP Coordinator, Revex Group
Before: Existing Platform Could Not Mitigate Production Related Challenges
- Revex Group was running the business using the accounting software that could not perform pre dispatched inspection and detect quality issues
- The stock was mismanaged and the production process lacked visibility that incurred unbudgeted costs and production
- Documentation and other processes were done manually using excel
- No accurate and up-to-date reporting hindered strategic and day-to-day decisions
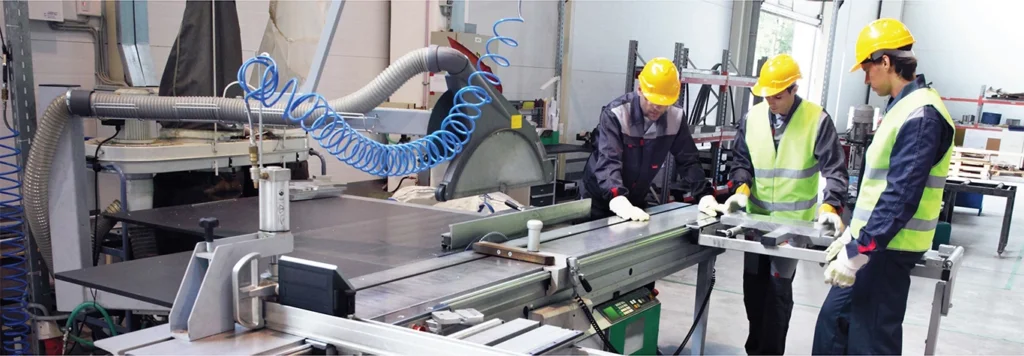
WHY SAP & UNEECOPS
- SAP Business One offered essential business management tools to track raw material to testing to finished goods
- Uneecops team proposed QC Add-Ons to Revex Group by learning the ongoing challenges of maintaining high-quality standards in the chemical industry
- Uneecops team closed the implementation cycle in 6 months merely
After: Improved Productivity And Quality Standards With Digitization
- QC add-on helped Revex Group improve quality standards by eliminating manual processes and allow the automation of QC for materials inwards, in-process and finished goods.
- WIP valuation was introduced after implementing SAP Business One that gave clear visibility into the value of stock stored, inprocess and value of raw materials available, thereby improving production planning
- Real-time data capture enables accurate reports via central online dashboards, giving managers the business intelligence they need to make fast, informed and actionable decisions well in advance
Efficiency gains
Quality Management
Mitigate multiple issues related to quality checks, ensuring products are made as per the chemical formula and standards
Stock Management
Better stock management with WIP valuation lowered costs that were earlier incurred due to lack of stock visibility